3D printed Patient specific Implants in India
A revolution in the implant industry was created with the fast and reliable production of patient-specific implants (PSI) to fix bone and skull defects.
Overview
A revolution in the implant industry was created with the fast and reliable production of patient-specific implants (PSI) to fix bone and skull defects. PSI is a rapidly emerging clinical treatment for various bone deformities including injuries due to accidents, war casualties, tumours, aesthetic requirement, functional improvisation, and congenital anomalies. Titanium which is being used for a long time but Polyetheretherketone (PEEK) provides excellent clinical outcomes along with numerous advantages.Graft3D's 3D printed patient-specific implants (PSI) allows the construction of almost any complex design geometry, which cannot be manufactured using other technologies. 3D printed PSI offers high-temperature performance, chemical resistance, fatigue resistance,and lightweight.
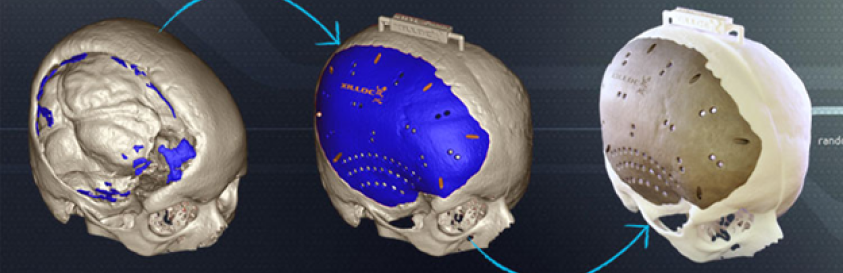
Benefits
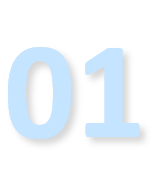
Reduced / lesser operation time
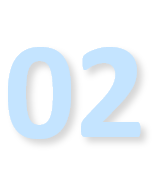
Fast recovery after surgery
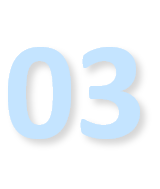
High aesthetic and reconstructive result
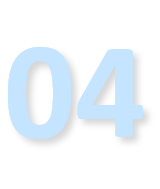
Outstanding
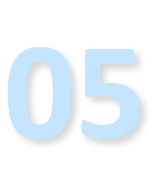
Made up of biocompatible material. Non-contact scanning process.

Implantable & detachable prosthesis . Rapid medical prototyping
Surgeon Perspective

Surgeons provide a detailed medical scan through a secure platform
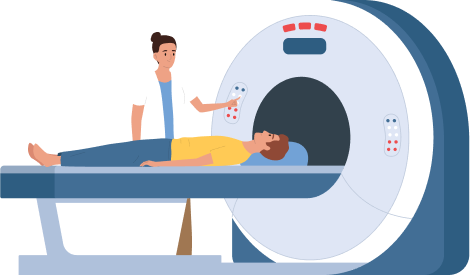

Graft3D analyzes the provided medical scan and generates a comprehensive quotation based on the complexity of the case and the required 3D printing material and process.
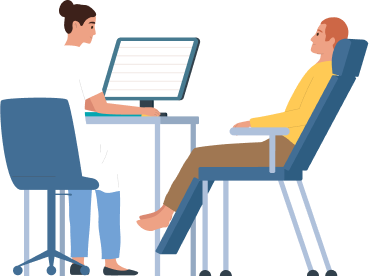

Once the scan is evaluated, a cost estimate is generated. The surgeon reviews and approves the quotation
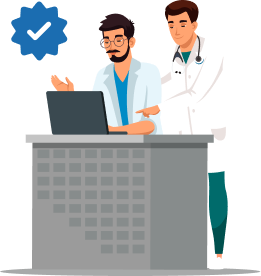

Graft3D: Segmentation & Modeling
Using advanced medical segmentation software is utilized to isolate the affected region from the scan. This data is then used to create an accurate 3D model, ensuring a customized and patient-specific implant.
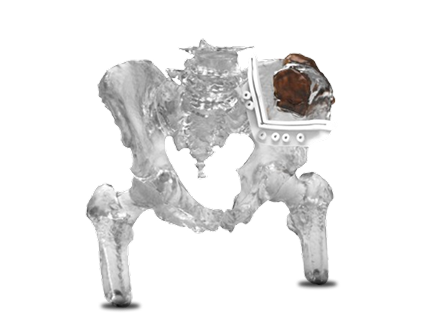

A preliminary implant design is shared with the surgeon for approval. Any necessary modifications or changes can be requested to ensure a perfect fit for the patient.
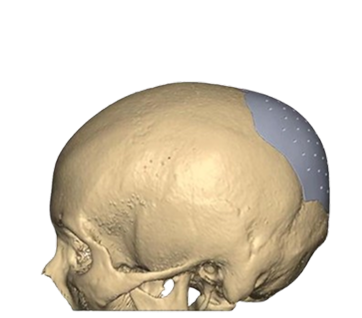

After the design confirmation from the surgeon we will 3D print the implant in the requested material and process. Implants go through medical (ISO) Standards before shipping.
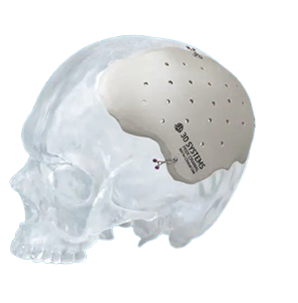

The final implant is securely packaged in a container and shipped, ensuring scheduled arrival for surgery .
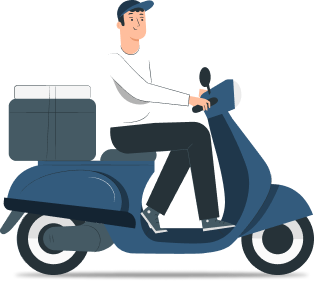

Once the implant is received, autoclaves the implant and ensure it is ready for the surgery. After the surgery, surgeon evaluates the implants and gives feedback to Graft3D
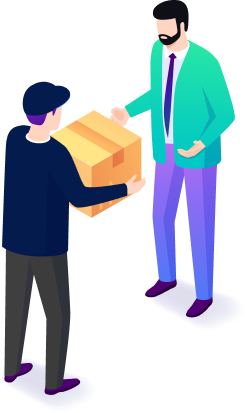
Our Clients
Testimonials
Our recent Healthcare 3D service projects, such as Medical 3D image segmentation and Bio CAD modeling for 3D printing, serve as a testament to our proficiency and dedication in providing outstanding 3D services. Whether you require image segmentation, bio CAD modeling, or comprehensive medical 3D printing solutions, we have all your needs covered.

Doctor
We use advanced software to preprocess images, such as noise reduction or contrast enhancement. This step ensures the input image is of the best quality for segmentation.

Doctor
We use advanced software to preprocess images, such as noise reduction or contrast enhancement. This step ensures the input image is of the best quality for segmentation.
Our Blogs
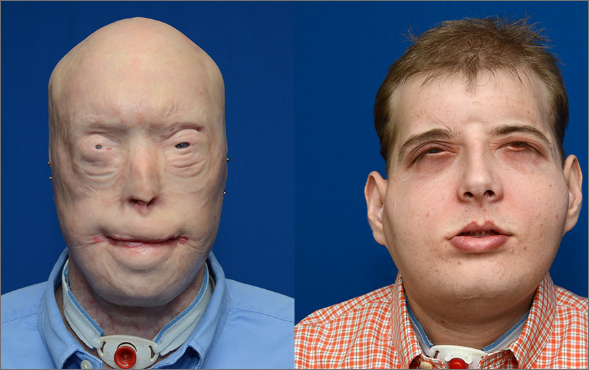
Virtual Surgical Planning Assists With Full Face Transplant
Admin
June 28 2021
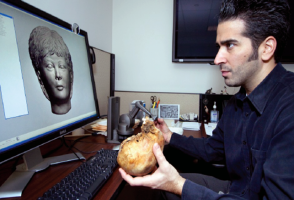
Geomagic Freeform Puts a Face To Missing Children
Admin
June 28 2021
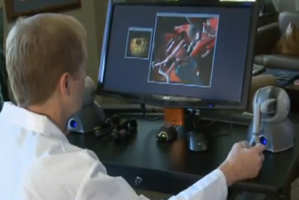
Geomagic Phantom Haptic Devices Allow Surgeons to Practice Procedures Using Virtual Touch
Admin
June 28 2021
FAQs
For designing and manufacturing patient-specific implants we require the following information from surgeon’s side:
1. Patient’s radiological data (Usually CT)
2. Filled order form, including specifications for implant design, delivery, etc. After contacting us, the surgeon will get an order form that has to be filled, and CT scanning protocols with recommendations for scanning parameters.
Conversion of DICOM To STL > Virtually Planning and Designing Using Geomagic Freeform >3D Printing the Titanium implant > Post Operative OPG
Patient-specific implants are manufactured using the following technologies and materials: Additive manufacturing (3D printing) technology DMLS (Direct Metal Laser Sintering), material: medical titanium alloy Ti6Al4V ,FDM ( Fused Deposition Modeling) , Material : PEEK ( Poly-Ether-Ether-Ketone).
The lead time to design and manufacture a patient-specific implant or surgical guide depends on the complexity of a clinical case and the surgeon’s requirements for the device. Typically, the delivery terms (after the surgeon approves the final design) are approximately 2 weeks for implants, and 1-2 weeks for surgical guides.
There is a provision in our Web Page, where you can fill the Details of the patient and upload their DICOM files. ( Please Give the Link Of < Get Quote > )
Yes, we can design and manufacture patient-specific implants in a shorter than usual timeframe. Please contact our team for your special needs.
Healthcare 3D Printing Service In India (Online Platform )
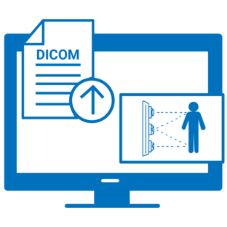
Upload DICOM Image OR 3D scan
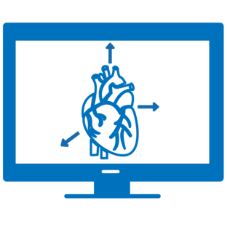
Convert your DICOM image to 3D files
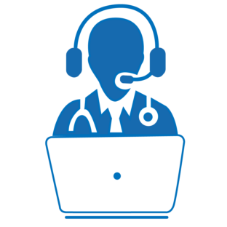
Consult Our Doctors & Bio CAD Modellers To Design Patient Specific Medical Devices
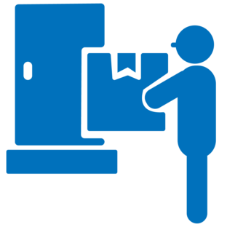